by Rudy Ramos, Mouser Electronics
In 1957, the Soviet Union launched Sputnik 1. The satellite was just 50cm wide. Today’s most massive unmanned spacecraft, the bus-sized Hubble telescope, weighs 11 tons. However, in recent decades, practical satellites have shrunk once more to Sputnik dimensions.
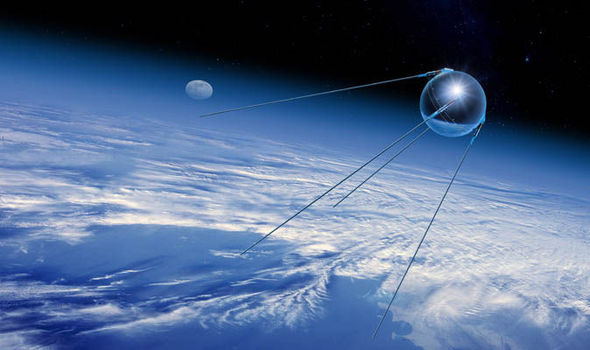
Several factors limit satellite minimum sizes; solar panel area to generate power and a big enough antenna for reliable communications. However today, more efficient electronics are reducing power needs, shrinking antennas, and solar panels. Sputnik 1 did little more than beep regularly, but small satellites now achieve far more.
Shrinking the satellite
These new class of satellites bear a confusing plethora of names; microsats, cubesats, tubesats, smallsats, phonesats, nanosats, picosats, and femtosats. Definitions are vague, but all emphasize minimal size, weight and power consumption. A ‘standard’ 1U cubesat is about 10x10x10cm and 1.3kg; a picosat could be as light as 0.1kg.
Tiny satellites are cheap to build and launch—bringing satellite capabilities to small companies, university departments, and even individuals. However, for better-funded developers, there’s are other advantages; the opportunity to respond quickly to changing demands—moving from concept to launch in months, unlike traditional spacecraft. Moreover, by the time a traditional satellite launches, its components may be a decade behind the leading edge.
The downside of fast, cheap development is high failure rates and short lifetimes. The hope is that microsatellites make up in quantity what they lack in quality.
Key developments making smallsats possible are falling launch costs; cheap, high-performance commercial off the shelf (COTS) hardware; and research from decades of government-funded space projects.
Low Earth Orbit (LEO) launch costs are around $15,000 to $50,000 per kg. Microsat launch costs are usually subsidized by the launch mission’s primary customers or by governments, but there’s hope of reducing real costs below $5,000/kg within decades.
Getting ready for space
Orbital spacecraft suffer temperatures from -180C to +130C passing from sunlight to the Earth’s shadow. Designers consider regularly shutting down systems outside their stable operating range (batteries are particularly susceptible to permanent damage from extreme temperatures). Spinning the spacecraft evens out heating, and heaters and sunshades also help. Sealed components, like batteries and capacitors, can swell or burst in a vacuum. This may not disable them but can reduce performance, and outgassing can damage other components.
Fortunately, pressure and thermal tolerances are easily tested on the ground. A general principle, borrowed from consumer electronics development, is that—for most components—moving quickly to burn-in testing produces more reliable devices than overly-cautious component pre-selection.
While spacecraft are at risk from cosmic rays and solar particles, low-cost microsats are usually in low earth orbit (LEO), between 160 to 2000km, where the Earth’s magnetic field provides significant protection. LEO satellites are also within the ionosphere, creating enough drag to bring them back down to Earth within a few months or years. For these reasons, permanent damage from charged particles is improbable.
However, brief glitches are common; a cosmic ray can flip a memory bit, for example. Robust software and hardware designs can recover from such random faults. A cheap, basic precaution is a simple watchdog timer that forcibly restarts the whole system every few hours.
ECC memory, which is highly-resistant to single bit errors, is an excellent example of a commercial off-the-shelf (COTS) technology that avoids a common failure mode at negligible cost. Controller Area Networks (CAN bus), used in the automotive industry, and the Internet of Things (IoT) concepts offer vibration and shock resistance and distributed fault tolerance. A robust system not only resists exotic space hazards but can also keep working, to some degree, despite common hardware failures, design errors and software bugs.
Learning from mistakes
There’s much to learn from past successes and failures. NASA has published considerable research on the suitability of COTS hardware for spaceflight.
Communication bugs and design limitations have waylaid several micro satellites. One cubesat project from a US company failed because its communication antenna was stowed beneath solar panels during launch, but mechanical issues prevented those panels from fully extending. The obscured antenna sent intermittent weak signals to controllers, but no practical communication was possible.
Last year, a trio of Australian cubesats were feared lost because solar batteries took longer than expected to recharge, never accumulating enough power to unfold communication antennas. However, ground controllers eventually recovered the spacecraft by borrowing a powerful transmitter dish that reached the undeployed antennas and uploaded new software.
The final frontier beckons
Frequent failures are both a challenge and an opportunity. Small satellite developers are still working out how to achieve with tens of thousands of dollars what NASA does with hundreds of millions. In fact, the implicit research goal of many microsats is gaining experience in making small satellites more reliable—that knowledge is often the most commercially valuable reward. The small satellite field is wide open for bold experimenters.
Leave a Reply