First reported in the 1940s, Metal Whiskers (MW) are spider-web-thin conductive filaments that sprout (most often) from tin, zinc, and cadmium metal surfaces. A “tin whisker” can be manually formed with poor soldering techniques, but metal whiskers actually grow on their own, too. They are a phenomenon that many engineers are not aware of. Silver, gold, lead, indium, and other metals have also grown whiskers. Hair-like metal structures erupt out from one or several grains of a metal surface. The whiskering transport mechanism is due to “grain boundary diffusion” (the explanation of which would require a foray into materials science and will not be attempted here).[i]
Perhaps the phenomenon is generally referred to as Tin Whiskers (TWs) because tin seems to be more plentiful and more likely to grow whiskers. Whatever the reason, metal whiskers grow over time, providing a short circuit path between metal-plated surfaces. In the 1950s and ‘60s, Bell Labs experimented with elements across the periodic table to determine if adding some other element to tin would dampen whisker growth. They found that adding 0.5 – 1% by weight of lead works, although other elements seemed to increase whiskering.
Jack Ganssle, in Embedded Muse 350, points out that, “Older solders were a mixture of lead and tin, and the lead seems to drastically mitigate (though does not entirely eliminate) whiskers. Remove the Pb, as we’ve done to comply with RoHS, and whiskers can grow. Modern components are so small, and SMT parts have such a tiny lead pitch, that TW shorts are even more likely.” Metal whiskers have been found on relays, connectors, ceramic chip capacitors, bus bars/rails, RF enclosures, circuit breakers, potentiometers, mounting hardware (e.g., nuts), and even the axial leads of a diode.i
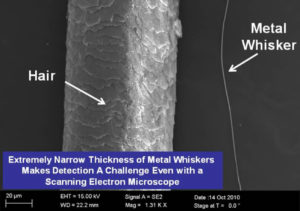
Being so thin, shouldn’t metal whiskers just burn up?
You would think that metal vapor arcs would be the most common result. Not quite; metal whiskers can carry tens of milliamps before melting. NASA missions have failed and reactor plants shut down due to tin whiskers. Heart pacemakers have been recalled due to tin whiskers. Tin whiskers may not always short a circuit but can cause on-going, difficult-to-determine issues. Whiskers do not need a PCB, connector, or active current/voltage sources to form, either. Data centers have had issues with zinc whiskers under raised floor tiles in server rooms. The whiskers under the floors are benign and can be left in place, but like asbestos, disturbing the material is the problem. Whiskers can become airborne and get lodged in nearby equipment.
The growth process of whiskers starts with an unpredictable incubation period of minutes to years, followed by a period of growth as fast as 15 nanometer per second to 1 mm per year.[ii]
Metal whiskers can cause:
- intermittent shorts if Iwhisker > Imelt; or, rule of thumb: current is available to the whisker on the order of greater than tens of milliamps
- permanent shorts if Iwhisker < Imelt; or, rule of thumb: available current to the whisker is less than tens of milliamperes
- metal vapor arcs are initiated in a vacuum when the voltage is more than dozens of volts and current is greater than tens of amps. In this case, arcs are capable of withstanding hundreds of amps of current before vaporizing.
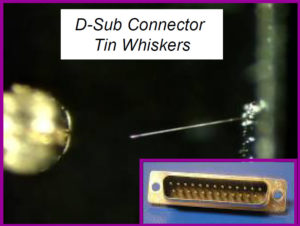
What can we do about tin whiskers?
No one has been able to eliminate whiskering, as the phenomenon is not yet fully understood. NASA advises avoiding pure Tin or Zinc if possible. Metal whiskers are tough to see with the naked eye. In areas where metal whisker “infestations” are possible, such as raised floors in server rooms, people should protect their lungs from breathing in loose whiskers and perform inspections away from vulnerable equipment. E.g., take floor tile, place it metal-side up, and inspect it with a laser or bright light while looking parallel to the floor tile surface against a dark, non-reflective backdrop. It doesn’t have to be a floor tile, however. Whiskers can form on shielding, plated housings or chassis, or between any metal surfaces.
According to Lyudmyla Panashchenko of NASA Goddard Space Flight Center, who has been working on metal whiskering problems for years, there are no clear-cut rules we can follow to eliminate whiskering. We can only reduce the risk of whiskers forming by avoiding the use of whisker-prone surfaces such as pure tin, zinc, or cadmium. A brass (Cu-Zn alloy) substrate under tin has shown a higher propensity to whiskering, as have materials with a significant mismatch of Coefficient of Thermal Expansion (CTE) to that of tin during periods of temperature cycling.
Panashchenko’s recommendation is to “trust but verify” the manufacturers by using X-ray Fluorescence (XRF) or Energy Dispersive X-ray Spectroscopy (EDS) if you are to be certain of the materials involved. Otherwise, conformal coatings can slow whisker growth or block whiskers from electrically shunting distant conductors. Lastly, you can remove or replace tin, zinc, or cadmium finishes if it is practical to do so. A hot solder dip with lead-tin (Pb-Sn) solder may not always be an option, however.
The miniaturization of electronics is cause for concern with respect to whiskers. A millimeter-long whisker is enough to short two pins; lower currents and voltages can cause permanent short circuits if whiskers do not melt. Metal whiskers might be causing inexplicable failures. To date, no one knows what exactly initiates whisker growth. We do know that the atoms of the surface metal that supply a whisker can come from a good distance away from the area of whisker growth, as there is little depletion of material in the vicinity of the whisker growth. We also know that whiskers grow outwards from the surface with additional material gathering at the base, not the tip. Regardless, the factors that initiate whisker growth are unknown, even after nearly 60 years of research on the topic.
[i] L. Panashchenko, “The Art of Appreciating Metal Whiskers: A Practical Guide for Electronics Professionals“, IPC Tin Whisker Symposium, Dallas, TX, April 2012
[ii] J. Brusse, M. Sampson, “Zinc Whiskers: Hidden Cause of Equipment Failure“, IEEE IT Professional Magazine, 2004 Nov/Dec, Vol. 6 No. 6, pp 43-47
Interesting. As a student I was given the job of temperature-cycling mobile radio tranceivers. I discovered the problem of whisker growth like this then. Another issue was conductive links between components caused by beads of water containing dissolved solder flux forming between transistor terminals. On of these keyed on the transmitter and I experimented with turning off the transistor with a resistor. I had to get down to ohms before I could get it to turn off.
The only fix we had for both problems was to coat the boards with a conformal coating. The only electronic device I have with conformal coating on its PCBs is my Lenovo laptop!
Any indication that dielectric grease, applied to connectors, affects TWs?
At 79 yo I still learn every day, whiskers were for sure the reason for a few electronic problems I found during my long professional work.
The problem on soldered parts it’s quite well known and very dependent on soldering composition and application technology but new for me as the cause for “virtual” cc
Please let we know the progresses of your investigation